本發明具體涉及一種城市污泥高溫炭化制備生物炭的工藝方法,屬于污泥處理技術領域。所述的工藝方法,包括6個步驟,分別為污泥除臭處理、污泥高溫炭化處理、污泥低溫干化煙氣處理、熱能動力源供應、污泥高溫炭化廢氣處理和高溫煙氣余熱利用。本發明所提供的工藝方法,科學合理,簡單易行,具有效率高、處理量大、安全節能、無二次污染和處理徹底的特點。
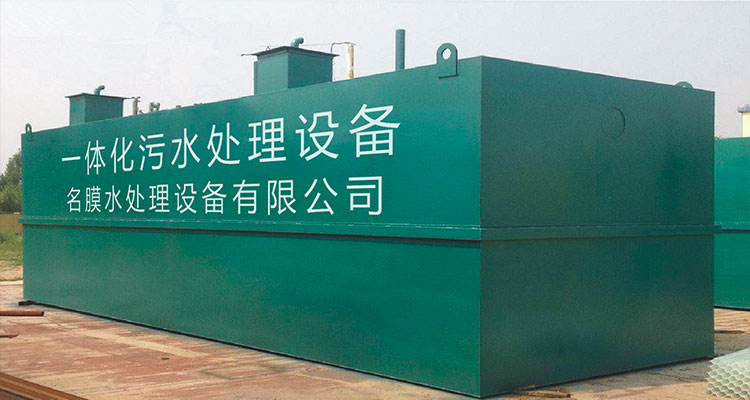
權利要求書
1.一種城市污泥高溫炭化制備生物炭的工藝方法,其特征在于:包括如下6個步驟:
S1:污水廠污泥進入污泥反應池,反應后產生臭氣,臭氣依次進入化學洗滌塔和除臭設備1,最后經尾氣處理塔排出;
S2:經步驟S1后的除臭濕污泥進入帶式壓濾機,得到除臭干污泥;除臭干污泥進入造粒機,制得顆粒狀污泥;顆粒狀污泥進入低溫帶式干燥機,得到的干化污泥先進入稱重干污泥料倉,再進入高溫炭化爐;得到的生物炭經水冷螺旋輸送機進入稱重生物炭料倉;
S3:步驟S2中,低溫帶式干燥機產生的煙氣先進入除塵設備1中,再進入噴淋塔1,降溫后進入尾氣處理塔后排出,噴淋水沿外排線排出;
S4:由天然氣作為熱力源進入焚燒爐,產生的熱量進入低溫帶式干燥機;
S5:高溫炭化爐產生的污泥炭化廢氣先進入除塵設備2,再進入噴淋塔2,噴淋塔內產生的可燃氣進入步驟S4中的焚燒爐,噴淋水進入密閉油水分離池,產生的生物油也進入焚燒爐內;密閉油水分離池內熱水經換熱器冷卻后,得到的冷水再次進入噴淋塔循環使用;涼水塔內冷水經換熱器換熱后得到熱水再次進入涼水塔循環使用;同時,工藝需冷卻設備內熱水也經涼水塔冷卻,得到的冷水循環使用;
S6:高溫炭化爐產生的燃燒高溫煙氣進入余熱鍋爐,再進入空氣預熱器轉變為低溫煙氣后排出;空氣進入空氣預熱器轉變為低溫熱空氣后再進入蒸汽換熱器,最終以高溫熱空氣形式進入低溫帶式干燥機;同時,軟化水進入余熱鍋爐,產生的蒸汽進入蒸汽換熱器,冷卻得到冷凝水沿管道排出。
2.根據權利要求1所述的城市污泥高溫炭化制備生物炭的工藝方法,其特征在于:步驟S5中,噴淋水循環使用過程中水分會蒸發,密閉油水分離池水量會逐漸減少,從上部對密閉油水分離池進行補水,產生的臭氣進入除臭設備2,再進入尾氣處理塔后排出。
3.根據權利要求1所述的城市污泥高溫炭化制備生物炭的工藝方法,其特征在于:步驟S2中,水冷螺旋輸送機內熱水分別進入稱重生物炭料倉和稱重干污泥料倉,稱重生物炭料倉和稱重干污泥料倉內冷水都沿管道進入至涼水塔內。
4.根據權利要求3所述的城市污泥高溫炭化制備生物炭的工藝方法,其特征在于:涼水塔內冷水又沿管道進入水冷螺旋輸送機內。
5.根據權利要求1所述的城市污泥高溫炭化制備生物炭的工藝方法,其特征在于:步驟S1中,污水廠污泥含水量為90-96wt.%;步驟S2中,除臭濕污泥含水量為90-96wt.%,除臭干污泥含水量為75-82wt.%。
6.根據權利要求1所述的城市污泥高溫炭化制備生物炭的工藝方法,其特征在于:步驟S2中,顆粒狀污泥在低溫帶式干燥機內干燥溫度為75-85℃,得到的干化污泥含水量為18-24wt.%;在高溫炭化爐內,炭化溫度為550-650℃。
7.根據權利要求6所述的城市污泥高溫炭化制備生物炭的工藝方法,其特征在于:步驟S2中,顆粒狀污泥在低溫帶式干燥機內干燥溫度為80℃,得到的干化污泥含水量為20wt.%。
8.根據權利要求1所述的城市污泥高溫炭化制備生物炭的工藝方法,其特征在于:步驟S2中,除臭濕污泥通過螺桿泵進入帶式壓濾機;除臭干污泥通過螺旋輸送機進入造粒機;顆粒狀污泥通過蛇形刮板輸送機進入低溫帶式干燥機。
9.根據權利要求1所述的城市污泥高溫炭化制備生物炭的工藝方法,其特征在于:步驟S2中,干化污泥通過蛇形刮板輸送機進入稱重干污泥料倉。
說明書
城市污泥高溫炭化制備生物炭的工藝方法
技術領域
本發明具體涉及一種城市污泥高溫炭化制備生物炭的工藝方法,屬于污泥處理技術領域。
背景技術
隨著我國城市化進程的加快,污水處理廠興建速度以及污水處理能力和處理率都呈現大幅度增長態勢。而污泥作為污水處理的“衍生品”,隨著污水處理量的增加而急劇增加。
污水處理工藝運行過程中,產生的污泥一部分回流作為生物反應的反應物,剩余的污泥則排出到系統之外,這部分污泥產量非常龐大。污泥成分比較復雜,除含有大量的水分外,還含有大量的有機質、難降解有機物、多種微量元素、病原微生物、寄生蟲卵和重金屬等成分,并伴有惡臭。污泥中含有大量的有機物和豐富的氮磷鉀等營養物質,會造成水質的富營養化,導致水質惡化,同時污泥中的重金屬、有毒物質、致病菌等也會給人類健康帶來極大危害。污泥不經妥善處理而任意排放和堆置,將對周圍環境、大氣、土壤、地下水資源等造成嚴重污染。
現階段,城市污泥處理的主要方式有:濃縮、穩定化、脫水、填埋、干化、焚燒和堆肥,更有未經處理的,由于污泥中含有大量微生物細胞和有機膠質,脫水困難;有機物主要以固定形式存在,生物降解困難。這些傳統處理方式存在許多缺點,如處理率低、技術單一、設備水平落后和二次污染風險大等。
發明內容
針對現有技術的不足,本發明的目的是提供一種城市污泥高溫炭化制備生物炭的工藝方法,科學合理,簡單易行,具有效率高、處理量大、安全節能、無二次污染和處理徹底的特點。
本發明所述的城市污泥高溫炭化制備生物炭的工藝方法,包括污泥除臭處理、污泥高溫炭化處理、污泥低溫干化煙氣處理、熱能動力源供應、污泥高溫炭化廢氣處理和高溫煙氣余熱利用6個步驟,具體包括如下步驟:
S1:污水廠污泥進入污泥反應池,反應后產生臭氣,臭氣依次進入化學洗滌塔和除臭設備1,最后經尾氣處理塔排出;
S2:經步驟S1后的除臭濕污泥進入帶式壓濾機,得到除臭干污泥;除臭干污泥進入造粒機,制得顆粒狀污泥;顆粒狀污泥進入低溫帶式干燥機,得到的干化污泥先進入稱重干污泥料倉,再進入高溫炭化爐;得到的生物炭經水冷螺旋輸送機進入稱重生物炭料倉;
S3:步驟S2中,低溫帶式干燥機產生的煙氣先進入除塵設備1中,再進入噴淋塔1,降溫后進入尾氣處理塔后排出,噴淋水沿外排線排出;
S4:由天然氣作為熱力源進入焚燒爐,產生的熱量進入低溫帶式干燥機;
S5:高溫炭化爐產生的污泥炭化廢氣先進入除塵設備2,再進入噴淋塔2,噴淋塔內產生的可燃氣進入步驟S4中的焚燒爐,噴淋水進入密閉油水分離池,產生的生物油也進入焚燒爐內;密閉油水分離池內熱水經換熱器冷卻后,得到的冷水再次進入噴淋塔循環使用;涼水塔內冷水經換熱器換熱后得到熱水再次進入涼水塔循環使用;同時,工藝需冷卻設備內熱水也經涼水塔冷卻,得到的冷水循環使用;
S6:高溫炭化爐產生的燃燒高溫煙氣進入余熱鍋爐,再進入空氣預熱器轉變為低溫煙氣后排出;空氣進入空氣預熱器轉變為低溫熱空氣后再進入蒸汽換熱器,最終以高溫熱空氣形式進入低溫帶式干燥機;同時,軟化水進入余熱鍋爐,產生的蒸汽進入蒸汽換熱器,冷卻得到冷凝水沿管道排出。
所述的步驟S5中,噴淋水循環使用過程中水分會蒸發,密閉油水分離池中水量會逐漸減少,從上部對密閉油水分離池進行補水,產生的臭氣進入除臭設備2,再進入尾氣處理塔后排出。
所述的步驟S2中,水冷螺旋輸送機內熱水分別進入稱重生物炭料倉和稱重干污泥料倉,稱重生物炭料倉和稱重干污泥料倉內冷水都沿管道進入涼水塔內。
所述的涼水塔內冷水又沿管道進入水冷螺旋輸送機內。
所述的步驟S1中,污水廠污泥含水量為90-96wt.%;步驟S2中,除臭濕污泥含水量為90-96wt.%,除臭干污泥含水量為75-82wt.%。
所述的步驟S2中,顆粒狀污泥在低溫帶式干燥機內干燥溫度為75-85℃,得到的干化污泥含水量為18-24wt.%;在高溫炭化爐內,炭化溫度為550-650℃。
優選的,所述的步驟S2中,顆粒狀污泥在低溫帶式干燥機內干燥溫度為80℃,得到的干化污泥含水量為20wt.%。
所述的步驟S2中,除臭濕污泥通過螺桿泵進入帶式壓濾機;除臭干污泥通過螺旋輸送機進入造粒機;顆粒狀污泥通過蛇形刮板輸送機進入低溫帶式干燥機。
所述的步驟S2中,干化污泥通過蛇形刮板輸送機進入稱重干污泥料倉。
S2步驟中,除臭干污泥通過造粒機進行造粒,一是使干污泥形態保持大小均勻,受熱均勻,便于干化和炭化,二是能降低污泥在低溫干化和炭化過程中產生的粉塵。粉塵增多易對后續設備造成堵塞,當粉塵跟噴淋水相遇時,易形成污泥,尤其炭化粉塵相遇噴淋水會形成油泥,造成二次污染,新產物油泥處理難度更大,違背污泥處理的初衷。
S2步驟中,污泥干化選用低溫帶式干燥機,除便于降低污泥含水量外,還有利于鞏固污泥形態,減少顆粒狀污泥破損,降低污泥后續輸送和炭化產生粉塵含量。
為防止后續設備出現故障,前邊干污泥無法存放,設置稱重干污泥料倉,干污泥料倉可準確顯示進出料量,干化污泥在干污泥料中轉后進入高溫碳化爐,干化污泥炭化后成為高溫生物炭,含水率在3%以下,由于生物炭溫度較高,通過水冷螺旋輸送機冷卻輸送至稱重生物炭料倉。
所述的稱重生物炭料倉帶稱重模塊,可以準確顯示生物炭日產量。
物料干燥、炭化過程會揮發水分,部分水蒸汽隨著物料進入倉內,水蒸氣接觸到冷的料倉金屬壁時,水蒸汽冷凝在倉內表面,同時潮濕的干污泥揮發水分易冷凝;當物料停止輸送到倉內,倉內溫度會持續降低,當倉內空氣濕度較大時,會因溫度下降形成冷凝水,冷凝水使物料掛壁凝結,冬天溫度較低時,會出現物料凍結現象,因此料倉壁溫不易過低和溫度變化較大。S2步驟中,干化污泥和生物炭進入料倉后倉內溫度升高,冷水降溫生物炭變為熱水后流經干污泥料倉和稱重生物炭料倉外壁伴熱保溫,可以有效防止物料掛壁凝結和凍結問題的發生。
S2步驟中,除臭濕污泥因含水量較高,選用螺桿泵進行輸送,除臭干污泥選用螺旋輸送機輸送;顆粒狀污泥為最大限度保持污泥狀態,減少后續粉塵的產生,選用蛇形刮板輸送機,干化污泥同樣選用蛇形刮板輸送機進行輸送。
S4步驟中,選用焚燒爐作為污泥低溫干化的熱能動力源,焚燒爐可同時作為炭化廢氣的處理爐,提高其利用率。
S5步驟中,在S1步驟中污泥除臭分解有機物不徹底,殘留少量有機物,在污泥高溫炭化過程中殘留有機物被徹底分解,產生少量臭氣、可燃氣、油等不凝氣體。
進一步的,S5步驟中,污泥炭化廢氣中的粉塵由除塵設備除去,可燃氣、臭氣進入焚燒爐焚燒回收利用,油經噴淋水捕捉后一起流入油水分離池進行油和水的分離,油水分離池會含有少量臭氣和生物油異味,對油水分離池密閉后進行臭氣集中處理,防止臭氣溢出擴散;分離出的油送至焚燒爐焚燒,水經過換熱器換熱后循環流入噴淋塔進行噴淋,當油水分離池水量減少時對其進行補水。
更進一步的,S5步驟中,噴淋水和涼水塔提供的涼水在換熱器中進行換熱處理,涼水塔同時給工藝需冷卻設備提供循環涼水。
S6步驟中,天然氣燃燒產生的高溫煙氣先經過余熱鍋爐,與軟化水換熱后,軟化水轉變為含有高熱量的水蒸氣,高溫煙氣溫度依舊含有大量熱量,高溫煙氣再經過空氣預熱器對空氣進行一次換熱,高溫煙氣溫度大大降低后排出,一次換熱的低溫熱空氣再通過蒸汽換熱器與高溫水蒸氣進行二次換熱,溫度升高后的高溫熱空氣通入到低溫帶式干燥機內,蒸汽變為冷凝水排出,余熱充分利用。
與現有技術相比,本發明具有如下有益效果:
1.所述的工藝方法,對污泥處理過程產生硫化氫、氨氣、硫醇類等其他惡臭氣體采取預先集中處理和后期封閉處理的方法,對污泥臭氣處理徹底;
2.污泥干化前,污泥呈顆粒狀,受熱均勻,具有節約能源和減少粉塵的作用;且對污泥高溫炭化廢氣進行了無害化和資源化處理,節約能源,避免了二次污染;
3.在污泥處理過程對粉塵的有效處理,避免了與污泥高溫裂解油氣形成油泥,加大處理難度,造成污染;
4.對污泥處理過程中的有效能源進行充分回收利用,大大節約能源,降低生產成本;料倉帶稱重模塊,可精確顯示料重量,便于控制料流量、處理量及能耗;
5.本發明所述的工藝方法科學合理、簡單易行,具有節能減排、安全可靠、連續穩定且日處理量大的特點,同時能夠真正的實現污泥減量化、無害化、穩定化和資源化“四化”目標。